Test report: New material for turning by Walter
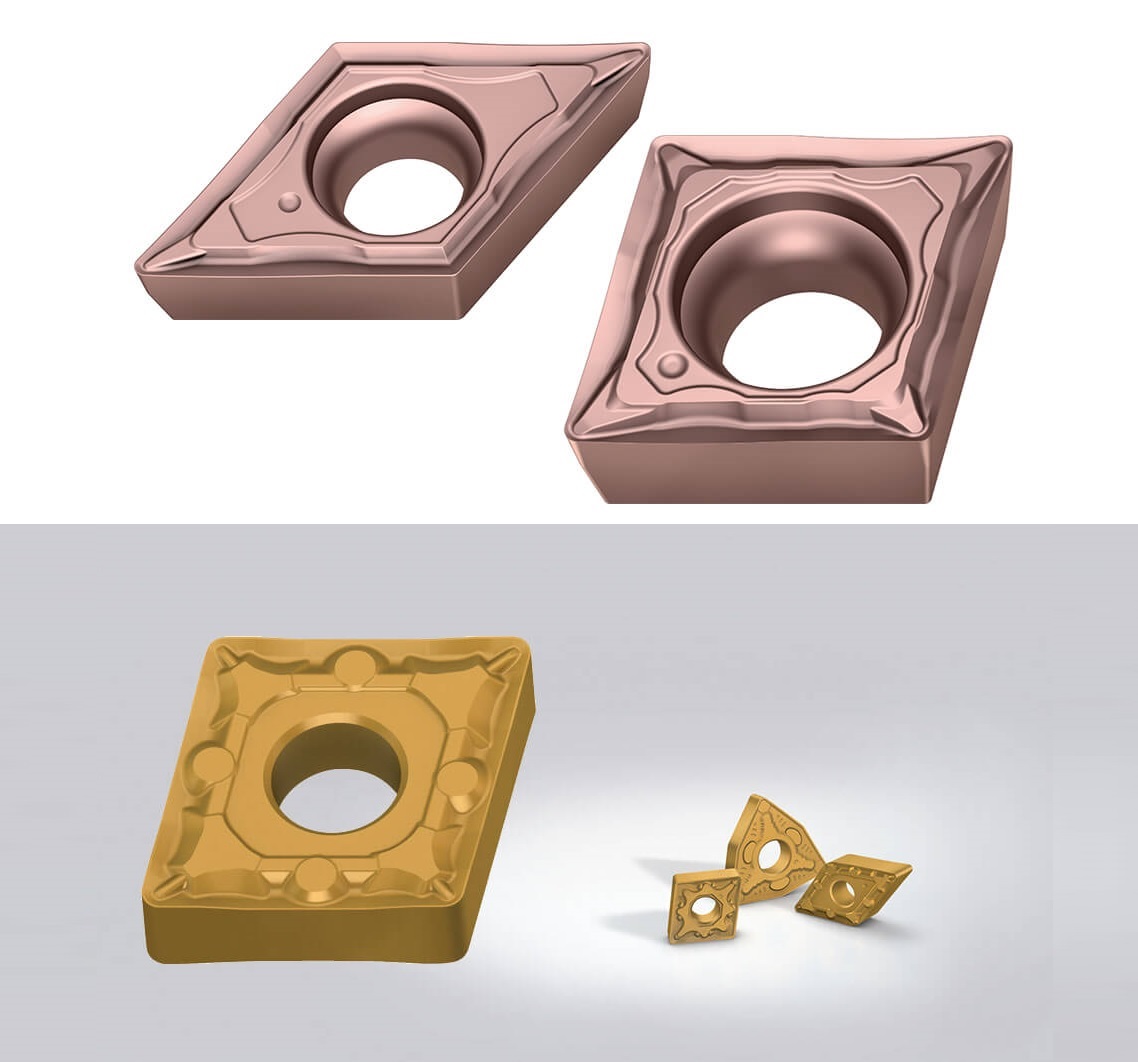
Introducing coated cermet and general-use carbide material turning inserts from Walter!
How is the performance compared to the inserts of manufacturers that is the top share in Japan?
Here is the durability test result to compare the performance.
INDEX
1.Outline
Finishing of carbon steel and alloy steel is a process that is likely to be subject to quality improvement that do not appear in numbers, such as improvement of dents and cloudiness. Using cermet is one option to improve cloudiness, but even Japenese manufacturers who have confident in cermet materials do not have a sufficient lineup. This time, the coating cermet material was newly introduced by Walter, and we tested a durability test.High-performance products are the main products for Western manufacturers, but Walter has introduced a low-priced general-use turning material that has high cost performance than Japanese manufacturers. We also tested it for durability.
2.Test report: WEP10C vs. Coated cermet made by Japanese manufacturer
-
Machine
Mazak QT-compact200MY -
Workpiece
Material: SCM420
Size: Φ80 x 100mm length
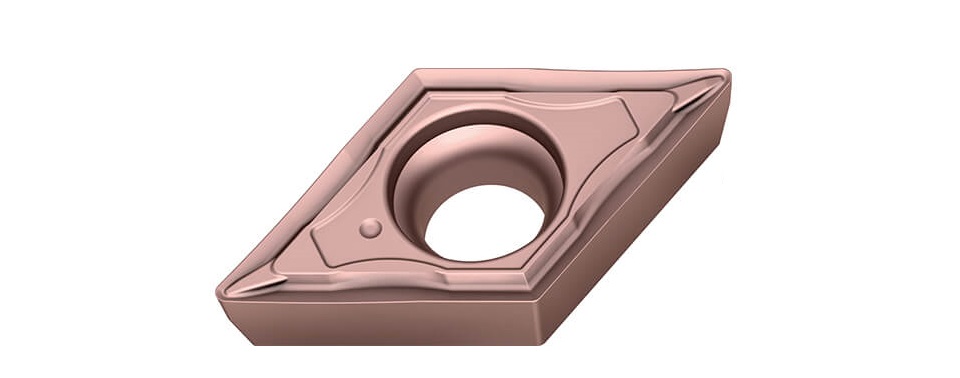
Insert for the test:
Tested durability with the cutting conditions that tend to use cermet.
(Finishing the shaft of small-diameter steel, which is difficult to increase peripheral speed even if you want to increase to the required speed. Expected about 6000 rpm for Φ10 workpieces)
Result:Walter's products had a better tool life than the products of manufacturers A and B, which is the top share in Japan.
Cutting condition: Vc=180m/min f=0.1mm/rev ap=0.5mm
With external coolant, Durability test for 60 min
Rake face wear condition
-
Walter
Material: WEP10C
FP4 breakerLess coating peeling and darkening on rake face.
-
Insert made by Japenese manufacturer A
Coated cermet
Finishing breakerLess coating peeling but machining heat would be high.
-
Insert made by Japenese manufacturer B
Coated cermet
Finishing breakerCoating is peeled and base material is exposed.
Flank wear condition
-
Walter WEP10C
No significant wear
-
Insert made by Japenese manufacturer A
No significant wear was seen, but there is a swelling that seemed to be welded.
-
Insert made by Japenese manufacturer B
Clearly wear
Good chips condition at all three companies
Chips were short at all three companies under the cutting condition of f=0.1mm/rev, ap=0.5mm. Chips of Japanese manufacturer A was quite short.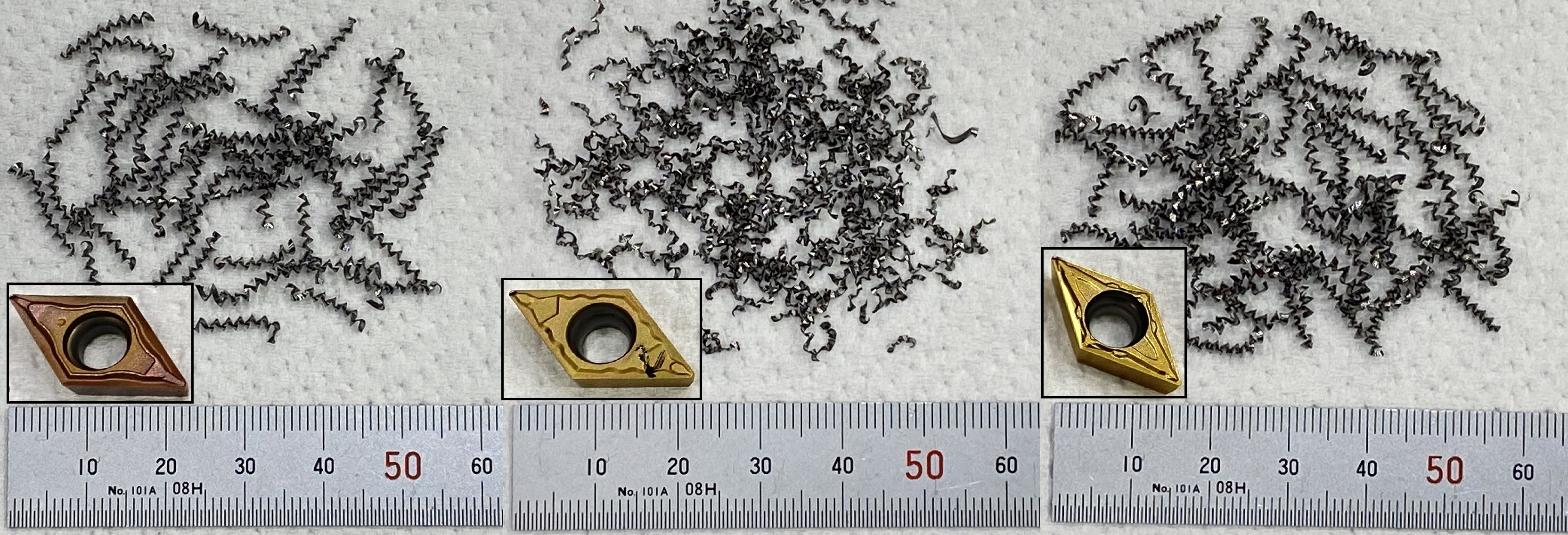
3.Test report: WPV10 vs. Coated carbide insert made by Japanese manufacturer
Result: Walter's products had a better tool life than the products of manufacturers A.Cutting condition: Vc=180m/min f=0.1mm/rev ap=0.5mm
With external coolant, Durability test for 60 min
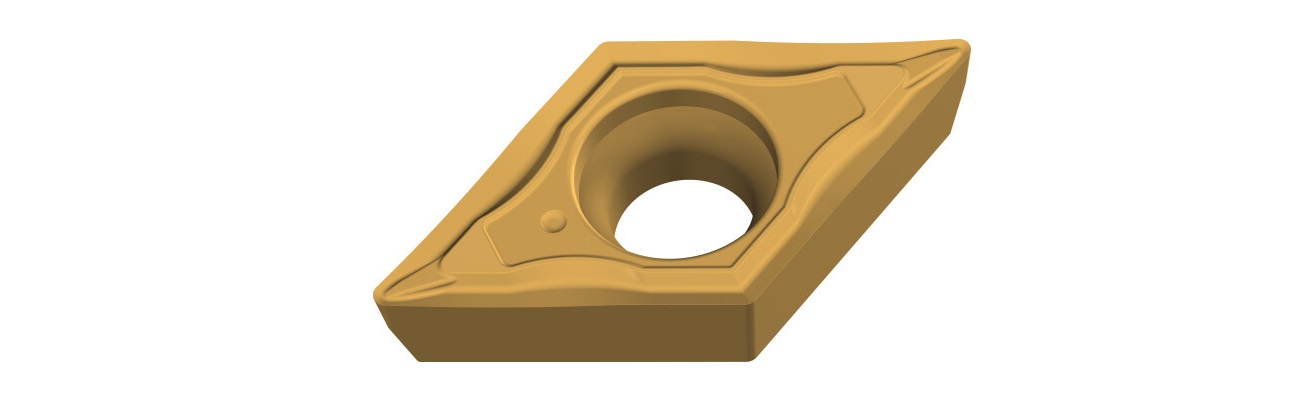
Insert for the test:
Insert of Japanese manufacturer: DCMT11T304(finishing breaker) New material for steels
-
Machine
Mazak QT-compact200MY -
Workpiece
Material: SCM420
Size: Φ80 x 100mm lengthMachine and workpiece are all the same as test of cermet.
Rake face wear condition
-
Walter WPV10 (General-use carbide material)
Chips seems to be hit to the breaker tip.
-
Insert made by Japenese manufacturer A
New material for material group of P
Less wear and darkening on rake face, but...
Flank wear condition
-
Walter WPV10 (General-use carbide material)
About 0.06mm wear
-
Insert made by Japenese manufacturer A
New material for material group of P
About 0.12mm wear.
Wears about twice as much as Walter.
4.General-use coated carbide price comparison
Competitive price than both overseas manufacturers and Japanese manufacturers.
Price comparison gragh for coating carbide material of each manufacturer
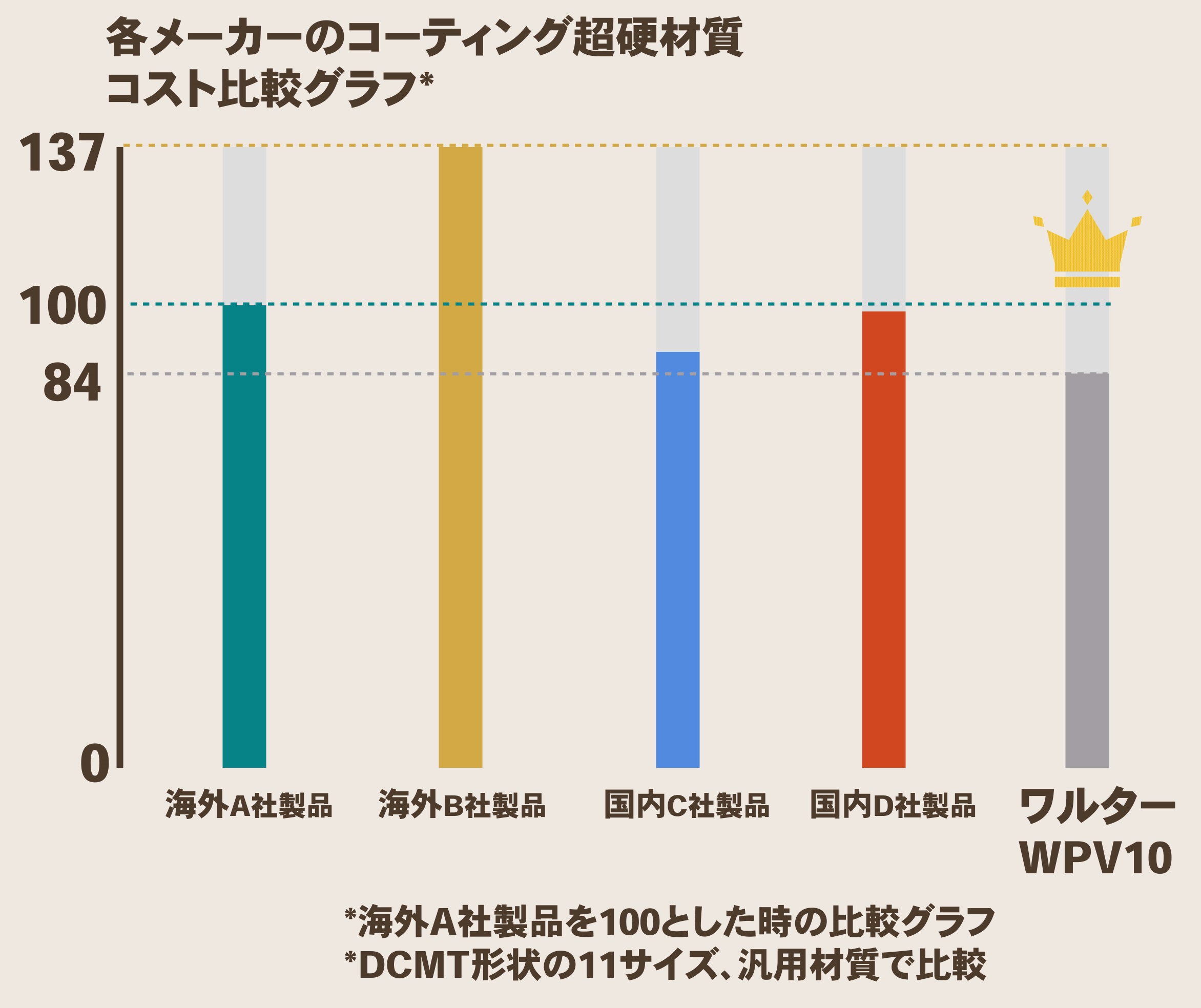
5.Explanation video
Explain the detail by comparing Walter and Japanese manufacturer.
This is an explanation video of this article
6.Supplementary information: Recommended allowance for finishing breaker
Testing with WET machining in addition to DRY machining in the video. Compare the chips under the cutting condition of Vc=180m/min, f=0.1mm/rev, ap=0.2mm, with external coolant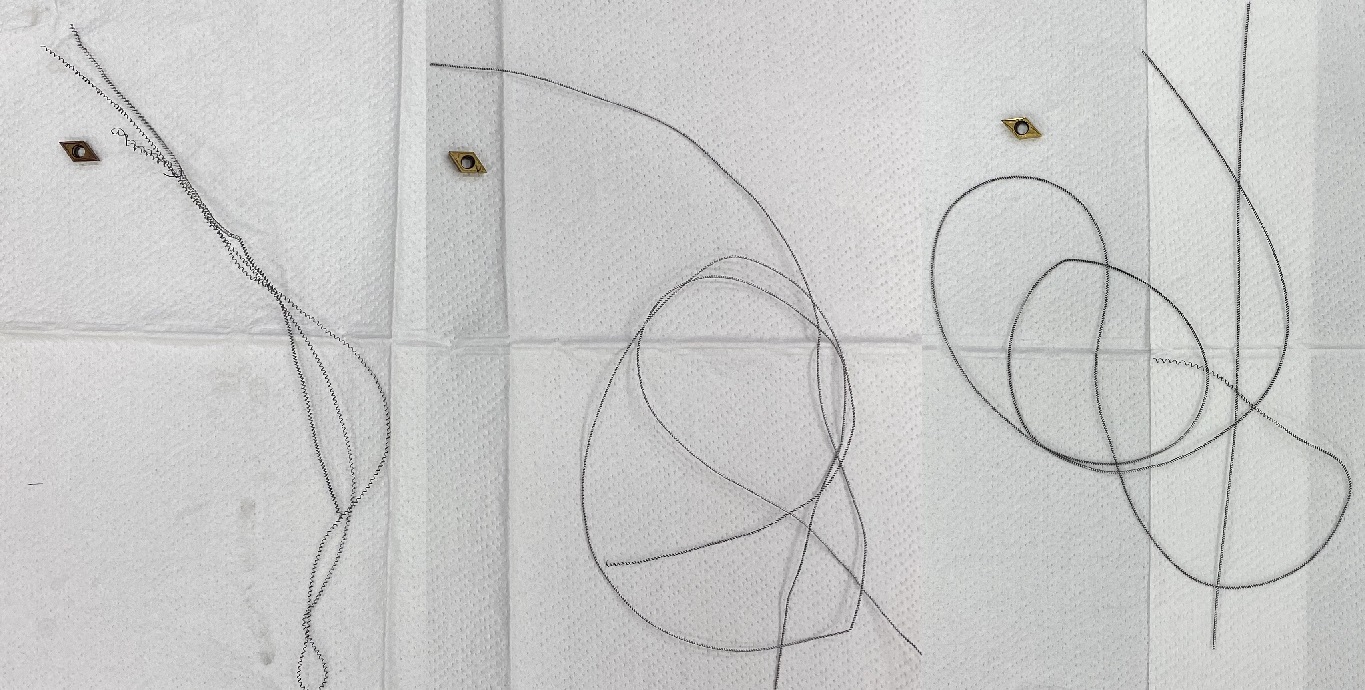
The curl of chip by Walter tool is slightly large, but chips are long with all inserts.
Even if it is the breaker for the smallest cut of the DCMT insert of Japanese manufacturer, the recommended depth of cut would be about 0.5 mm for WET processing.
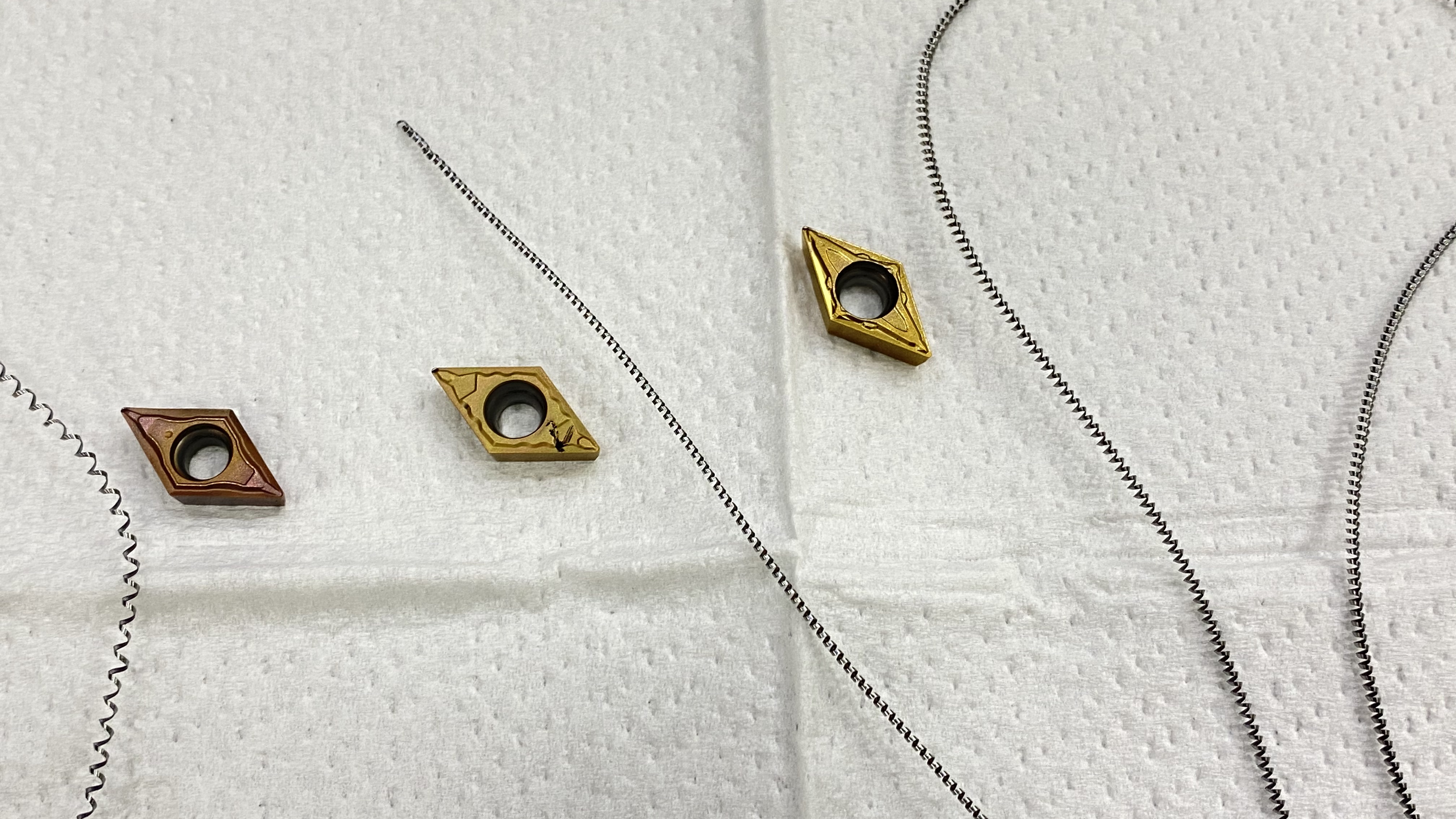